A world of learning.
Professional development, United States
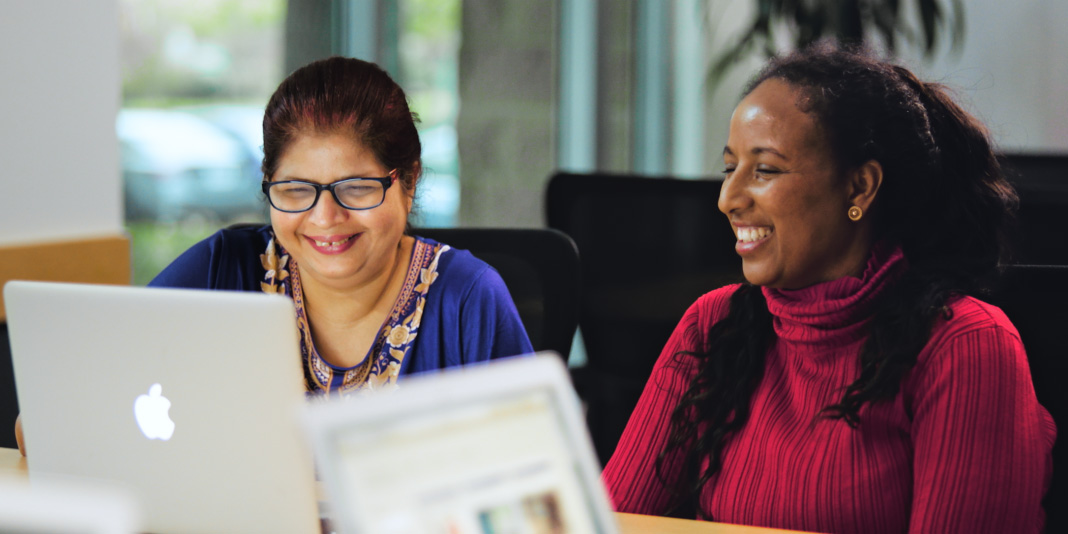
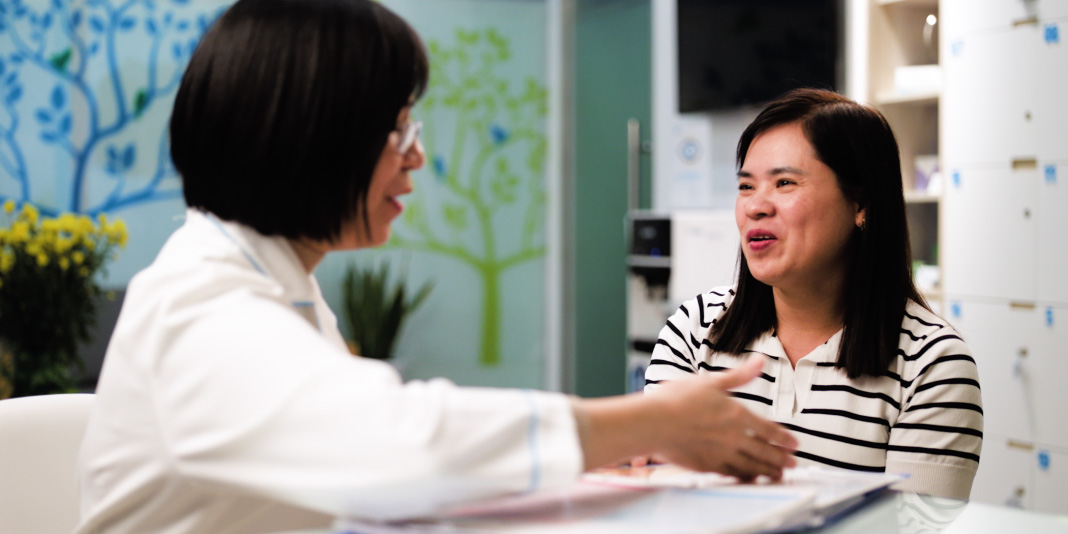
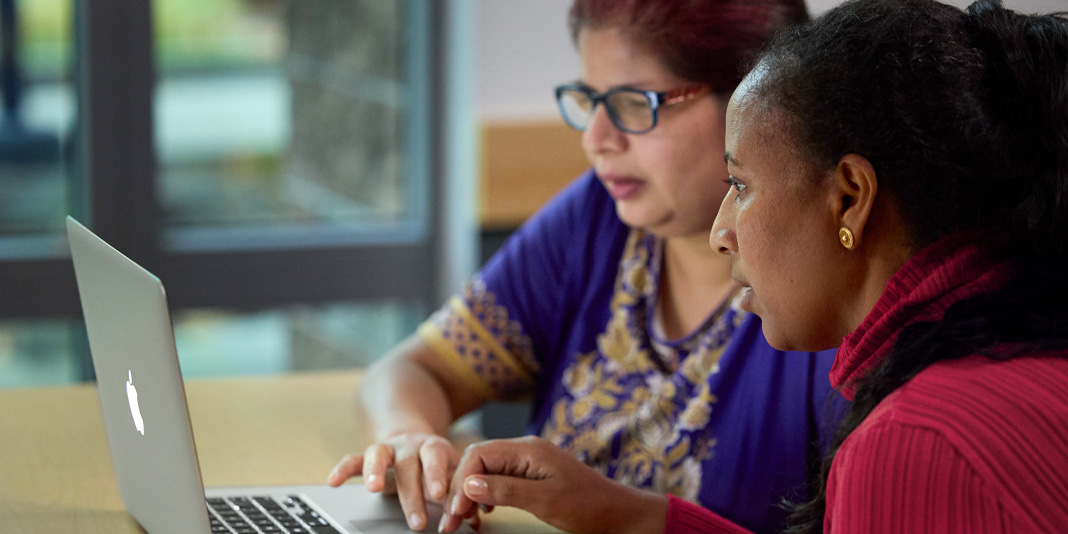
Feature
A world of learning.
Education is a powerful equalizing force.
The Apple Supplier Employee Development Fund is our $50 million commitment to further invest in the people in our supply chain — and to innovate and expand on our long-running education programs.
Through the Fund, supplier employees learn about their workplace rights and gain opportunities to develop new skills such as coding, smart manufacturing fundamentals, language learning, health training, and leadership development.
Since the Fund’s launch, we have delivered more than 5.7 million training and education sessions, with our programs reaching more than eight million people since 2008. Through the Fund, we are providing people all over the world with opportunities to advance in their jobs or explore new job paths.
More about Apple’s Supply Chain
-
People
We act on feedback.
Component manufacturing, China mainland
-
Education
Skills that open doors.
Robotics training, China mainland
-
Feature
Accountability from day one.
Logistics and repair, United States
Accountability
from day one.
Logistics and repair, United States
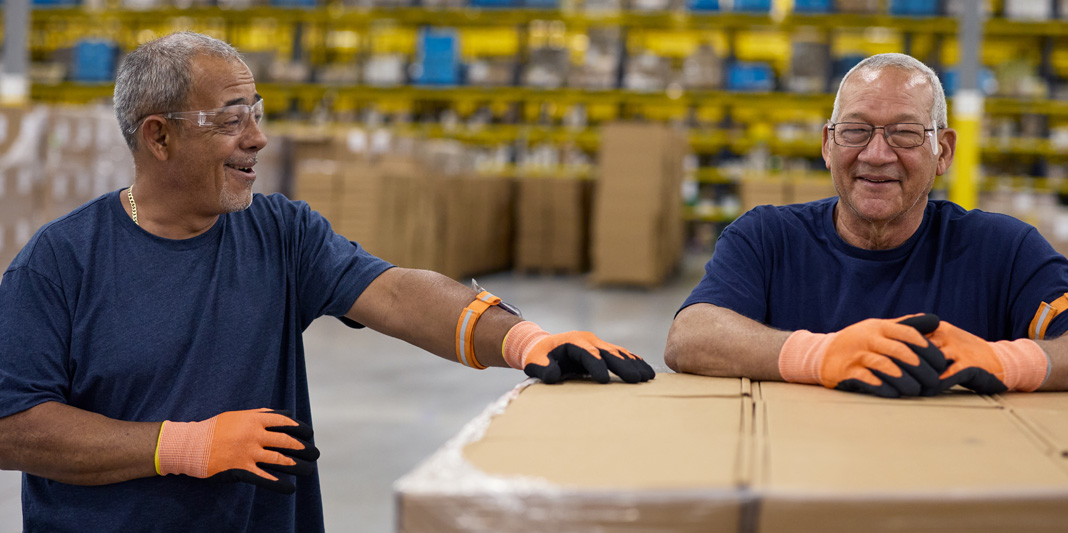
Feature
Accountability
from day one.
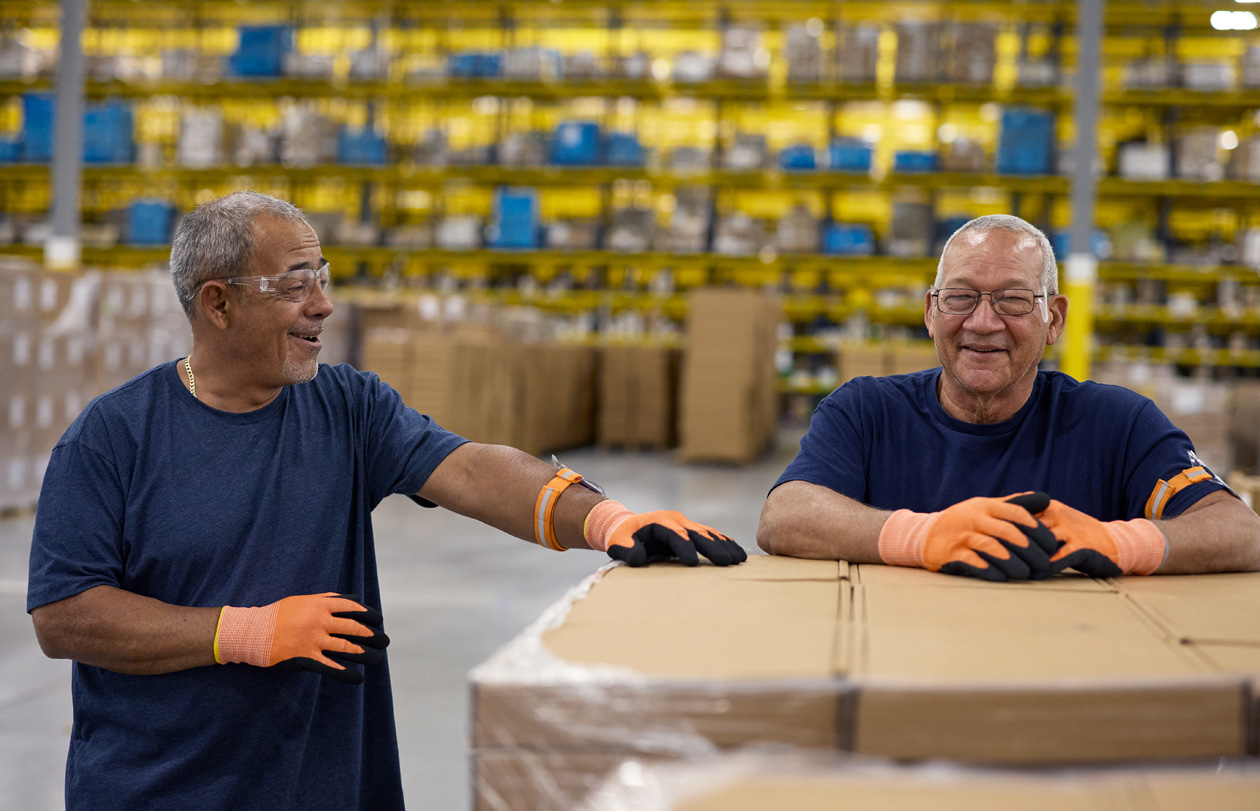
Logistics and repair, United States
Apple products are designed in California and made by people all over the world. Thousands of businesses and millions of people in more than 50 countries and regions are part of our supply chain, contributing their skills to help build, deliver, repair, and recycle our products.
Our suppliers are required to meet the strict standards of the Apple Supplier Code of Conduct, no matter where they operate or what type of goods, services, or labor they provide to Apple. The Code’s requirements cover labor and human rights, health and safety, the environment, ethics, and management practices.
We are committed to holding ourselves and our suppliers accountable to high standards. This includes working to make sure our strict standards are met before production begins, conducting regular assessments of our suppliers’ performance, and actively listening to supplier employees.
Assessments, conducted by independent third-party auditors, thoroughly examine a supplier’s operations through worker and management interviews, detailed site walkthroughs, and comprehensive documentation reviews. In addition to planned assessments, we also conduct unannounced visits, where the supplier has no advance knowledge of the auditor’s arrival.
How we hold suppliers accountable.
-
Check before work starts
Before we award business to a supplier or begin production, we check for any potential human rights, environmental, or other risks, and we work with them to address any issues found.
-
Listen to supplier employees
As part of our supplier assessment process, tens of thousands of confidential interviews are conducted with supplier employees about their workplace experiences.
-
Investigate reports
In addition to addressing the feedback we receive from supplier employees, we promptly investigate any allegations we receive, with Apple experts typically arriving onsite within 24 to 48 hours.
-
Take swift action
If a violation of our standards is discovered, we require suppliers to promptly implement a plan to correct it, and to strengthen their policies and procedures to prevent the issue from reoccurring.

-
893
assessments of supplier facilities conducted in 2024, with more than 22 percent being unannounced visits
-
125
new or expanding supplier facilities that were assessed in 2024 for their ability to meet our requirements before entering our supply chain
More about Apple’s Supply Chain
-
People
We act on feedback.
Component manufacturing, China mainland
-
Education
Skills that open doors.
Robotics training, China mainland
-
Feature
A world of learning.
Professional development, United States